Sheet Extrusion
- Home
- /
- Sheet Extrusion
Production process cast sheet Extrusion
During the process of extrusion of plastics, raw thermoplastic material in the form of small beads (resins) and/or regrind are gravity fed from a top mounted hopper into the barrel of an extruder. Additives such as colorants and UV inhibitors (in pellet form) are additionally used and can be mixed into the granulate prior to arriving at the hopper or added through a coextruder.
The material enters through the feed throat (an opening near the rear of the barrel) and comes into contact with the screw. The rotating screw forces the granule compound forward into the barrel, which is heated up to the desired melting temperature of the compounded plastic.
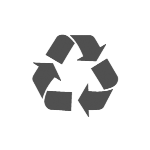
KΞΞN ®
By implementation of the principle of a Circular Economy, CSX wants to become one of the leaders in Europe in developing plastic sheet materials and film.
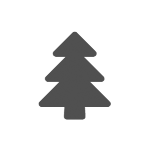
Sustainable
CSX is not only considering existing generations, but also future generations. Due to their environmentally friendly production process CSX is aiming to produce to state of the art sustainable standards and beyond.
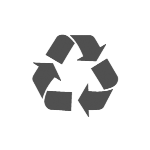
Clean
Environmentally friendly production processes are at the forefront of CSX. CSX strives for a system in which raw materials are fully re-deployed in a Circular Loop system.